Unit or output costing
Introduction The method which is used to ascertain the cost of a product or service is called costing.The method of costing differs from industry to industry.The unit is output costing is suitable...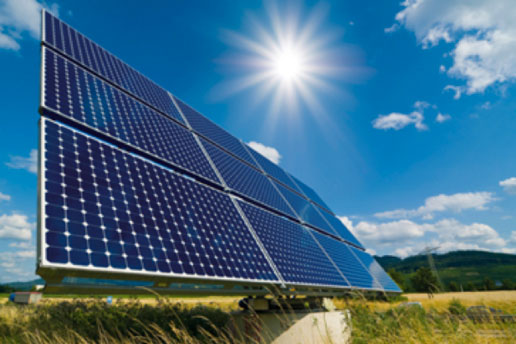
Cost sheet
Cost sheet is a sheet, which assemble the detailed costs in respect of a cost unit . It is prepared weekly,monthly or yearly to show details of the various elements of cost of the goods produced like prime cost, factory cost,etc.
Cost sheet presents cost information relating to production in such a manner that it shows cost of total production, quantity of production and per unit cost of production.
Importance of cost sheet
1. It helps to fix selling prices more accurately.
2. It helps in comparisons of cost of similar jobs or between costs of similar periods.
3. It gives information for compilation of estimates.
4. It provides useful information to trace wastages,losses and inefficiencies and thus affect economics.
5. It acts as a guide to the producer and helps in formulating a definite production policy.
Elements of cost sheet
According to natural characteristics,cost can be classified into three groups (a) material cost ,(b) labour costs and (c) expenses. They are known as elements of cost .
Each elements of cost :
1.Direct material: Direct materials are those materials,which can be identified with and allocated to cost unit conveniently. They become part of production. For example wood cost is direct cost for any furniture.
2. Indirect material: Materials used in manufacture of a job or a product which cannot be readily identified with, it will be indirect materials. For example cost of nails ,glue, polish,etc
3. Direct labour: Direct labour is the waves which can be conveniently identified with and allocated to cost units. These compromise wages paid to workers who are engaged to producing a product in a manufacturing concern.
4. Indirect labour: Indirect labour is the wage which cannot be conveniently with or allocated to cost units . It implies that the timenpaid for was not used for a particular cost unit but for work in general as , wages paid to the store keeper in a printing press
5. Direct expense: It consists of expenditure other than direct materials and direct labour which can be identified with and allocated to cost units. It is also called chargeable expenses.
Examples of direct expenses are :
1. Fees paid to architects of building
2. Hire of equipment for a particular job
3. Royalty paid , etc.
6. Indirect expenses: Indirect expenses are expenses which cannot be conveniently allocated to cost units. For example,(I) rent,rates, insurance of factory premises,(ii) depreciation and repairs of machine,etc.
Indirect expenses are divided into three groups:(I) factory overhead,(ii) office and administrative overhead (iii) selling and distribution overhead.
Components of unit costing (cost sheet)
1. Prime cost : The aggregate of all direct costs, which change with direct proportion to change in output,is called prime cost. It is the total of direct materials,direct labour and direct expenses.
Prime Costs = Direct Labor + Direct Raw Material + Direct Expenses
2. Factory or work overheads and cost:
It is the total prime cisf and factory or work overheads,which includes indirect material cost, indirect labour and indirect expenses of factory. It is also called manufacturing cost.
Factory cost = Prime cost + Factory overhead
Examples of items included in factory overheads include:
(I) Factory expenses (e.g., rent, rates, insurance, water, heat, and electricity)
(ii)Factory maintenance (e.g., cleaning, servicing, repairs, oiling, and greasing)
(iii)Depreciation of factory plant and machinery and buildings
(IV)Wages and salaries (other than direct labor) of persons engaged in the factory (e.g., foremen, supervisors, maintenance staff, factory administrative or clerical staff, testers, and examiners)
(v) Consumable stores and all forms of indirect material (i.e., material that cannot be traced as part of the finished product, such as oils and greases, small tools, cleaning materials, and minor spare parts for repairs)
Office overhead and cost of production
If office and administrative overhead are added to factory cost,then cost of production can be obtained. In other words, cost of production is the total of the factory cost and office and administrative overheads.
Cost of production= Factory cost+ Office and administrative overheads
All expenses incurred on the administration, direction and control of an organisation are collected and accumulated under ‘administrative overheads’. Staff salaries, rent, electricity, legal expenses, audit fee, director’s fees, rent and maintenance of office equipment, depreciation on office furniture and equipment and insurance thereof, etc. are all example of administrative overheads.
Cost of goods sold
If inventory of finished goods includes on cost of production,it is called cost of goods sold. It is calculated on addition of opening stock of finished goods of finished goods to cost of production and deduction of closing stock of finished goods.
Selling overhead and cost of sales or total cost
If selling and distribution overheads are added to cost of production,it is called cost of sales or total cost .
Total cost or cost of sales = Cost of production+ Selling and distribution overheads
under selling and distribution overheads. Selling costs are incurred in obtaining and retaining a customer. Sales office expenses, commission and salaries of sales force, expenses on advertising, publicity and show room, etc., constitute selling overheads. Expenses incurred on the distribution of products are called distribution overheads.
Items of selling and distribution overheads
1. Salaries, commission and travelling expenses of sales manager ,sales representative or agents and other sales staffs,
2. Showroom and exhibition or display expenses,
3. Advertisement expenses or display expenses,
4.Carriage Outward
5. Rent of ware house