MAIN STEPS IN CEMENT PRODUCTION
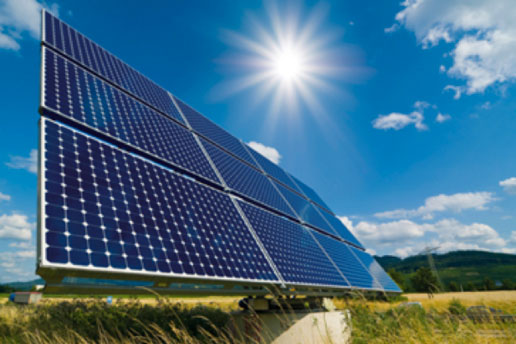
Cement is an extremely fine material having adhesive and cohesive properties which provides a binding medium for the discrete ingredients. It is a binder, a substance used for construction that sets, hardens, and adheres to other materials to bind them together. They are not very water-soluble and so are quite durable in water and safe from chemical attacks. Cement mixed with fine aggregate produces mortar for masonry, or with sand and gravel, produces concrete. Concrete is the most widely used material in existence and is behind only water as the planet's most-consumed resource. It is capable of bonding the constructional material like sand, stones, bricks, buildings, blocks and many more. The principal constituents of cement are the compounds of calcium, aluminium and silicon. Cement containing calcium is called calcareous whereas containing aluminium and silicon is called argillaceous. Cement has a unique property of setting and hardening of calcareous and argillaceous material underwater by virtue of certain chemical reactions.
Raw materials for cement production
1. Limestone (CaCO3)
2. Clay (SiO2, Al2O3 and Fe2O3)
3. Gypsum (CaSO4.2H₂O) 4. Magnesia (MgO) 5. Sulphur 6. Alkalies
1. Crushing: The raw materials are extracted from quarries by blasting, drilling or ripening using heavy machinery. The raw materials are then crushed in a rotating cylindrical ball or tube mill. The ores are crushed first to 6 inches and reduced them by a secondary crusher or hammer mill to 3 inches.
2. Grinding: The crushed ore is mixed. either in dry or wet ways is then grounded and then made homogeneous by means of compressed gas in a grinding mill. The resulting material is known as slurry having 35-40 % water.
3. Heating: Slurry is then introduced in a rotary kiln with the help of a conveyor. The rotary kiln consists of a large cylinder, 8 to 10 feet in diameter and a height of 300-500 feet. It is made of steel and lined with firebricks. In a rotary kiln, the slurry is passed through different zones of temperature. The whole process in kiln is completed in 2 to 3 hours. Different temperature zones
i. Preheating zone: In this zone, the temperature is kept to 500°C and usually the moisture is removed and clay is broken into silica, aluminium oxide and iron oxide.
ii. Decomposition zone: Temperature is raised upto 800°C. In this zone, limestone decomposes into quick lime and CO2 .
CaCO3 → CaO+CO2
iii. Burning zone: In this zone, temperature is maintained upto 1500°C and the oxide formed in above zone combines together and form respective silicate, aluminate and ferrite.
2CaO+ SiO2--------->2CaO.SiO2
3CaO+ SiO3--------->CaO.SiO2
3CaO+Al2O3--------> 3CaO.Al2O3
4CaO + Al2O3 + Fe2O3 ------>4CaO.Al2O3.Fe2O
iv. Cooling zone: This is last stage where the whole assembly is cooled upto 150- 200°C.
4. Final grinding: The product which is obtained from rotary kiln is called clinker. It is usually in the form of greenish black or grey coloured solid. It is then air cooled and required amount of gypsum is mixed with the clinker to slow down the setting of cement so that cement is adequately hardened.
5. Packing and Shipping: Cement is conveyed from grinding mills to silos (large storage tanks) where it is packed in 20-40 kg bags. Most of the product is shipped in bulk quantities by trucks, trains or ships, and only a small amount is packed for customers who need small quantities.